Hi,
I had a question about one of my earlier PCB design based on the NRF24L01+ wireless transceiver. This was a correct schematic, but the PCB design was not 'reference' and did not give a good signal, it was noisy and had dropouts. Based on feedback on this forum I concluded I best go with a reference design from the manufacturer. I have now done that and got some boards made. The layout is pretty much exact what the manufacturer recommends, but now I do not get any signal at all, but the chip does initialize properly.
Any ideas on how to troubleshoot this? Here is my pcb design, and below I'll paste the manufacturer reference design.
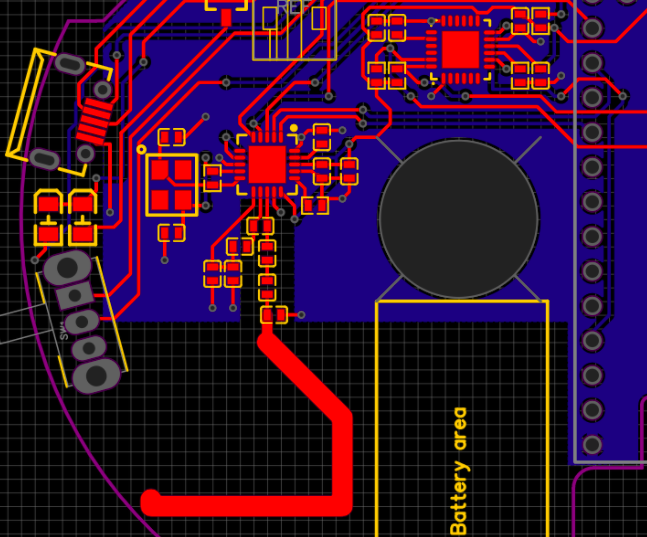
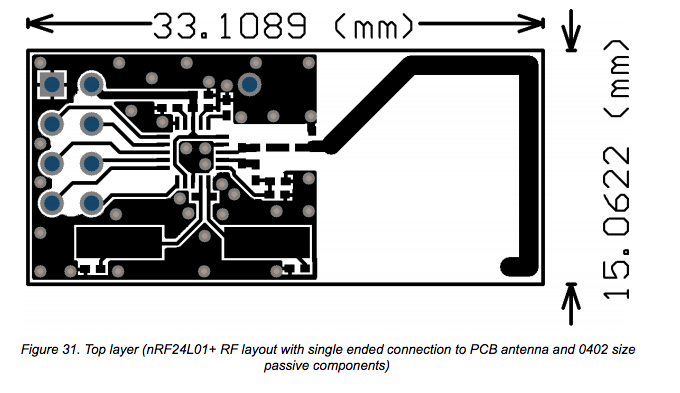
I have been reading up a bit about antenna design and fro what I gather the single ended antenna should be more forgiving than a MIFA (which I had before). I'm kinda stumped on where to go from here...
Tia for any guidance on troubleshooting.
Chrome
89.0.4389.82
OS X
10_13_6
EasyEDA
6.4.17