Hi,
I'm getting a via diameter DRC error but there is no error. It says my via diameters are less than the DRC diameters but both are set to 0.61mm.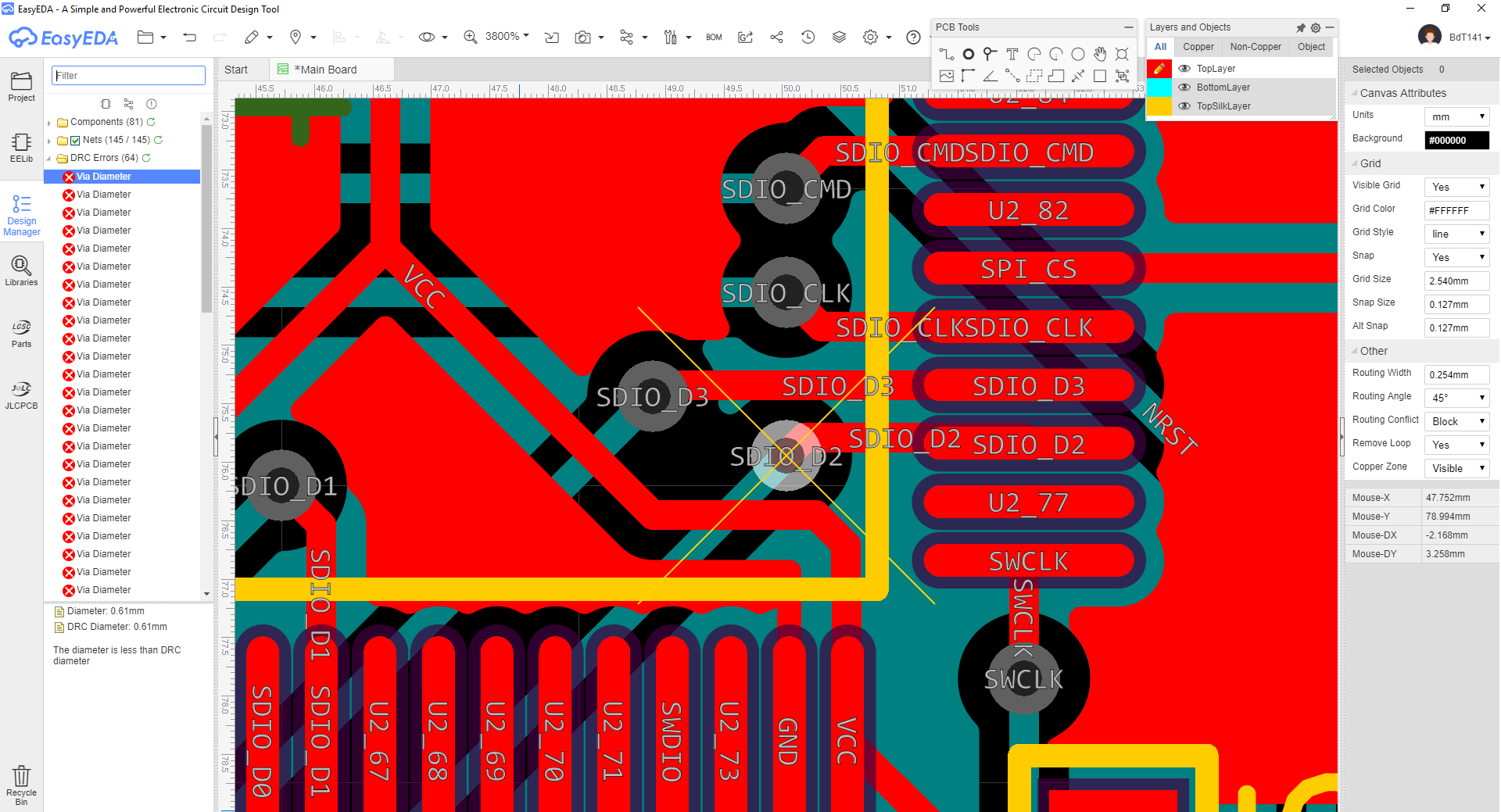
Electron
3.0.11
Windows
10
EasyEDA
6.1.41